The industrial revolution, characterized by fast technology changes, has created modern manufacturing and production on its backbone. What makes it all happen, though, is the printed circuit board (PCB), the element that allows for seamless functioning in an automated system. All of these, from the programmable logic controllers (PLCs) to robotics, work within the heart of industrial automation to make it efficient, precise, and reliable.
A high-quality PCB card plays a very vital role in industrial automation for providing the reliability and efficiency needed to ensure proper automated processes. Printed circuit boards constitute the heart of control units, sensors, and modules used in communication, through which accurate coordination and processing of data take place. Since they are made up of high-quality PCBs that are able to resist rough industrial conditions, such as high temperatures and vibrations, high-quality PCB cards endure wear and tear, performing optimally in manufacturing and robotics, among other automation processes.
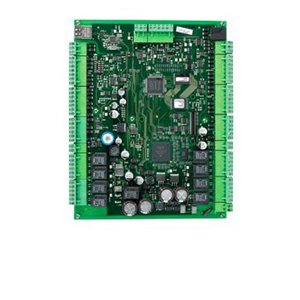
What is a PCB?
A printed circuit board is flat, made of insulating material in the form of fiberglass or composite epoxy. The flat board has conductive pathways etched onto it. In a PCB, various types of electronic components like microprocessors, resistors, capacitors, and sensors have pathways connecting them for work purposes. High-quality PCBs basically act as the spine of electronics, providing support and enabling structural strength and connectivity, further ensuring reliability and durability.
The Importance of PCBs in Industrial Automation:
Industrial automation means that the use of a control system such as computers or robots in the handling of machinery and processes in the production environment. Here, PCBs play a crucial role in the following ways:
- Advanced Control Systems:
PCBs are vital for the working of PLCs, which is like the brain of the automated systems. They process input from sensors, process data, and control output to actuators. In this way, they ensure accurate and efficient working. - Improving Robotics:
In robotics, PCBs are used for controlling movements, processing visual data, and managing communication between various components. The use of high-density PCBs enables compact and lightweight designs in modern robotic systems. - Supporting IoT Integration:
The Industrial Internet of Things (IIoT) depends on PCBs for connecting sensors, actuators, and communication modules. These PCBs enable real-time data collection, analysis, and remote monitoring, thus optimizing production processes. - Ensuring Reliability in Harsh Environments:
High-quality PCBs, for an industrial automation, are prepared to withstand extreme conditions- high temperatures, humidity and mechanical vibrations. It works consistently in harsh environments so that the downtime and maintenance cost decreases.
Types of PCBs Used in Industrial Automation:
- Rigid PCBs: Used mostly in control systems and machines, rigid PCBs ensure strength and stability.
- Flexible PCBs: Best for compact devices and systems where the wiring is complicated; they are flexible and can save space.
- Rigid-Flex PCBs: The benefits of rigid PCBs and flexible PCBs are combined in rigid-flex PCBs, which are used in advanced robotics and automation systems.
- High-Frequency PCBs: They are especially designed for high-speed communication and signal processing in IoT-enabled automation.
Key Advantages of PCBs in Automation:
- Miniaturization: PCBs allow various elements to be accommodated within a smaller space, meaning miniaturization and efficiency in equipment.
- Precision and Consistency: Automation requires high accuracy and PCBs ensure this in the electrical connections.
- Scalability: PCBs are tailored to fit any size industrial equipment, from smaller machines to large manufacturing units.
- Cost-Effectiveness: Mass production of PCBs minimizes the cost of manufacture and thus automation reaches many more industries.
The Future of PCBs in Industrial Automation:
With the evolution of technology, PCBs continue to adapt to the emerging trends, such as AI-powered automation, advanced robotics, and IIoT. Multilayer PCBs, new materials, and design techniques that improve upon earlier ones form the pathway to more efficient and sophisticated automation solutions.
Further, the integration of smart PCBs with communication modules and embedded sensors is sure to transform the future of industrial predictive maintenance and real-time monitoring. It will certainly increase productivity and help improve sustainability through the reduction of unnecessary waste and energy consumption.
High-quality PCBs are the unsung heroes behind the intelligence and efficiency of modern systems for industrial automation. Flexibility, reliability, and adaptability make them unavoidable when creating smarter, connected, and sustainable industrial operation. With the continued adoption of automation by industries, the work that PCBs do will only amplify the position they hold to ensure their place in furthering technological advancement.